Vahterus Units Keep Things Running Smoothly at Pölkky Wood Processing Plants
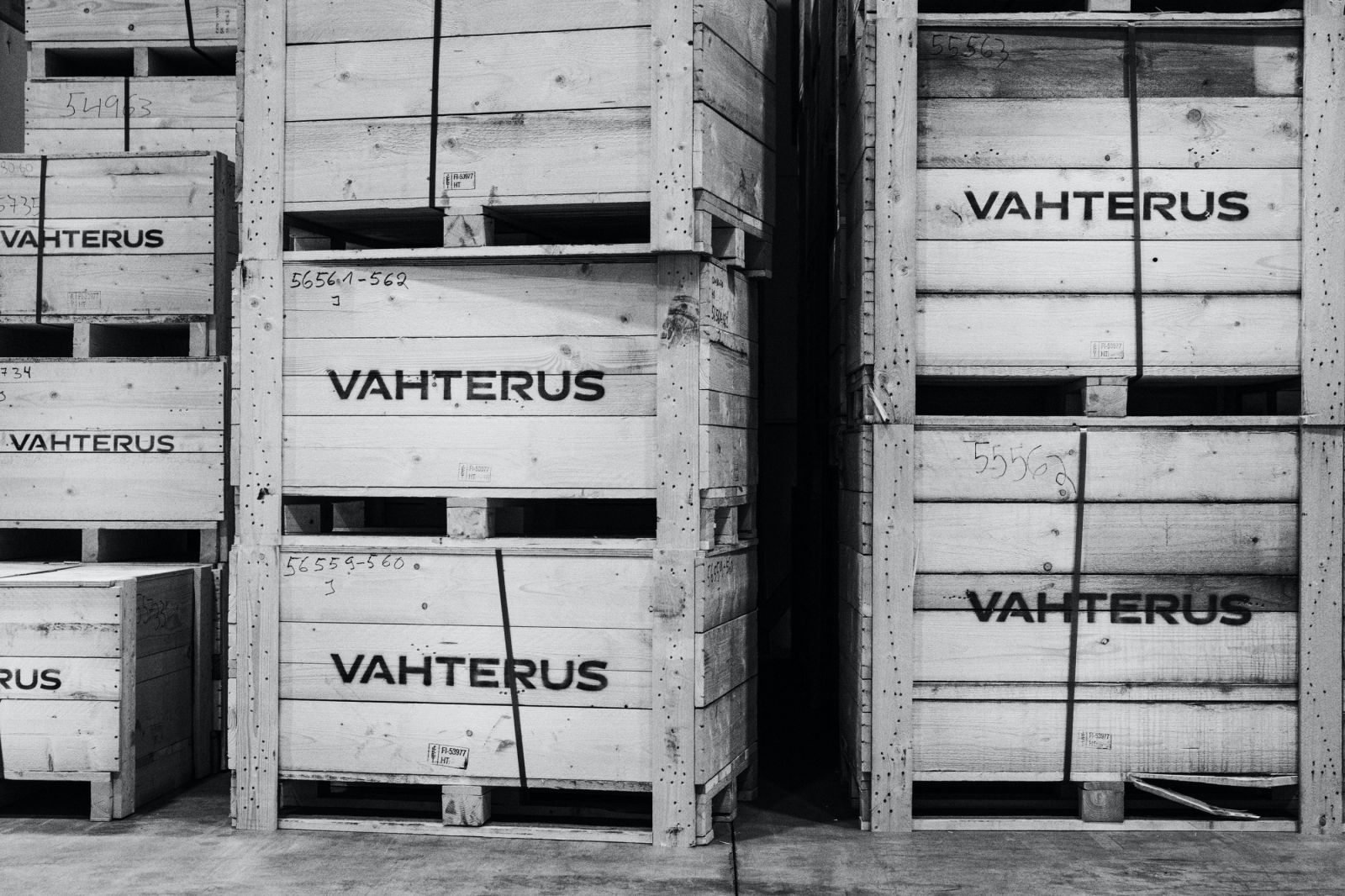
Founded in 1968, Pölkky is the largest privately owned wood-processing company in Northern Finland. The group’s sawmills and further processing plants are located in Taivalkoski and Kajaani in the heartland of Finnish raw wood, the municipality of Kuusamo. In 2017, Pölkky produced approximately 650,000 m2 of sawn timber with a group-wide turnover of €168 million. Modern wood-processing techniques and skilled personnel are the foundation of Pölkky’s high-quality products and efficient operations. In total, Pölkky Oy employs approximately 200 people. In addition to Pölkky, other companies in the group include Pölkky Metsä Kmo Oy, Kitkawood Oy and Kajaaniwood Oy with a combined staff of about 380.
In spring 2017, staff at Pölkky’s Taivalkoski production unit noticed that the tube heat exchanger located between the hot-water boiler and the district heating network needed replacing. Hot boiler water circulated in the exchanger’s primary side and district heating water in the secondary side. ”The heating plant had a roughly seven-year-old tube heat exchanger that was part of the original installation”, explains Pölkky’s Plant Service Manager, Arto Hannola. ”The exchanger didn’t run reliably and we had to goggle the tubes every couple of months. We wanted to improve the system’s reliability, so we started planning to replace the heat exchanger.”
The company contacted Vahterus, and staff members from both companies got together to discuss a tailored solution. The new heat exchanger would operate between the boiler and the supply network, and the aim was to protect the boiler from any supply water leakages and to improve its reliability in the event of a leak. Vahterus started the project by listening to what the client needed and then offered a unique solution designed specifically for this application. While most Vahterus projects start the same way, the cooperation between Vahterus and Pölkky was exceptionally tight.
During the procurement process, Pölkky delegates visited a reference site where the Vahterus unit made a lasting impression on them. Having considered different options together, the companies eventually chose to replace the old tube heat exchanger with a more compact solution, after which a fully welded 12-MW plate heat exchanger was installed in the Taivalkoski production plant. ”I had good experiences with a Vahterus exchanger in my previous job, so we started preparing the project based on this”, says Hannola. ”Eventually we placed the order and had the new exchanger installed, and we haven’t had any issues with the equipment since then.”
Vahterus Plate & Shell technology is ideal for power plant applications because the fully welded heat exchangers have no soldered joints or gaskets and the round shape allows them to withstand considerable heat stress. These features are crucial for units used in the varying conditions of boiler plants. Moreover, the compact size makes installation in power plants easier.
This autumn, a little over a year since the Taivalkoski upgrade, Pölkky decided to convert the direct connection between the boiler and district heating network in its Kuusamo unit into an indirect connection. The project requirements were the same as those for the Taivalkoski unit. ”In its current state, the boiler is directly connected to the district heating network, so by installing a heat exchanger between them, we can protect the boiler from any major leakages, as these could cause major damages to the boiler”, clarifies Hannola.
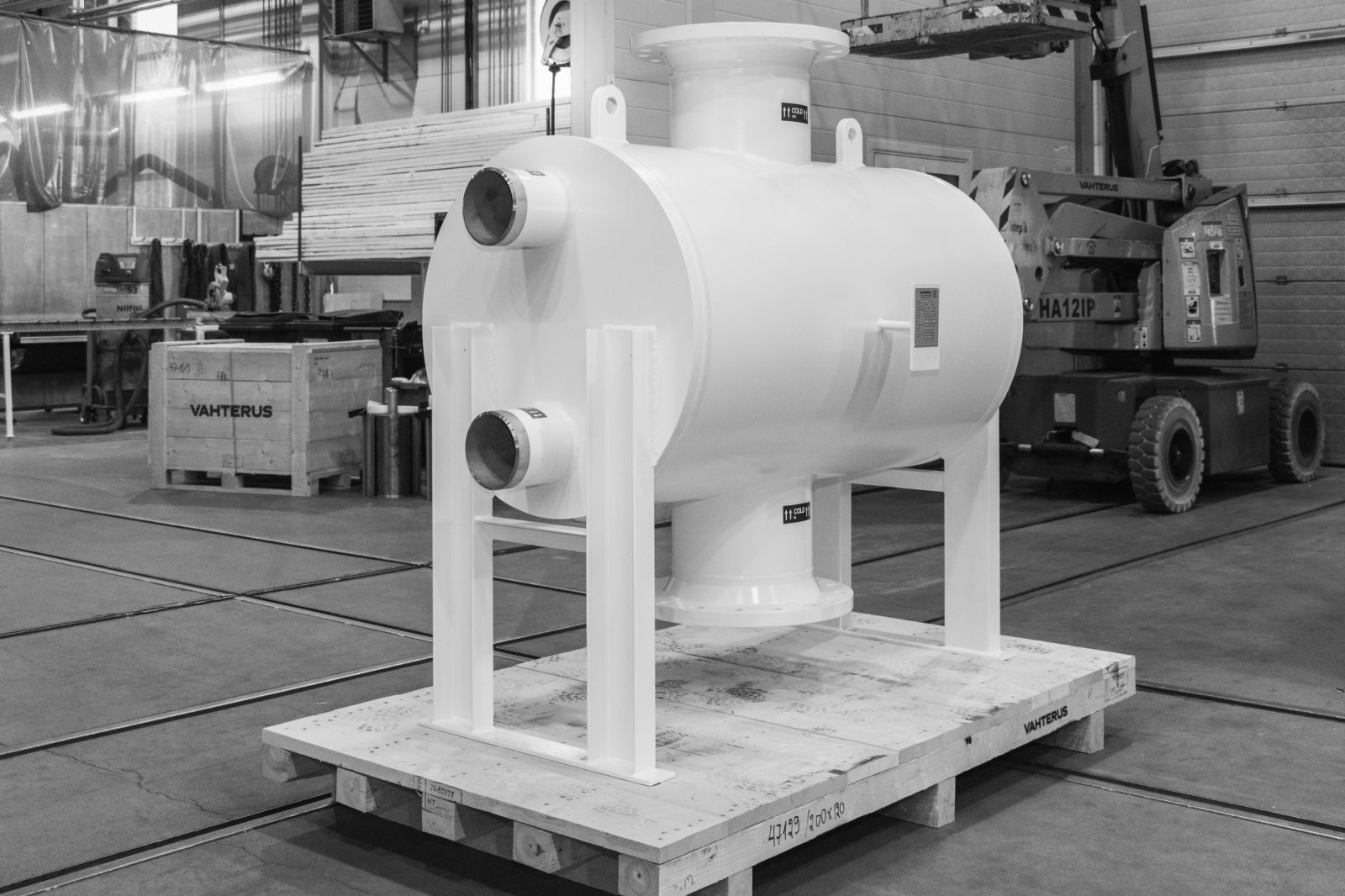
The direct connection was considered a risk since the Kuusamo plant is in operation year round, meaning that even short downtimes lead to production losses. After the positive experiences of the Taivalkoski unit, it was only natural that Pölkky would continue working with Vahterus. The companies therefore got together once again to discuss the best solution, and eventually a 12-MW water-to-water heat exchanger was tailored for the Kuusamo plant. In order to ensure reliable operation, an indirect connection was found to be the only option, even though indirect connections have traditionally resulted in losses.
Vahterus plate heat exchanger technology helps keep temperature differences extremely small, which minimises these losses. With the risk of losses eliminated, an indirect connection often turns out to be the best solution to ensure security of supply and efficient operation. This is because disturbances in the district heating network are not directly connected to the boiler, making it more reliable.
Vahterus Plate & Shell heat exchangers have been used to replace numerous old tube heat exchangers and gasket heat exchangers in order to improve a system’s reliability and make it easier to maintain. In applications like these, having a maintenance-free solution is a clear competitive advantage. Today, Vahterus heat exchangers can be found in several boiler plants, especially at large industrial sawmills. ”The Taivalkoski project was extremely successful, all things considered. The Kuusamo project has progressed to the order stage this autumn, and our plan is to have the new heat exchanger installed around the turn of the year. All in all, working with Vahterus has been a very satisfying experience for us”, Hannola concludes.
Download the case study as a PDF
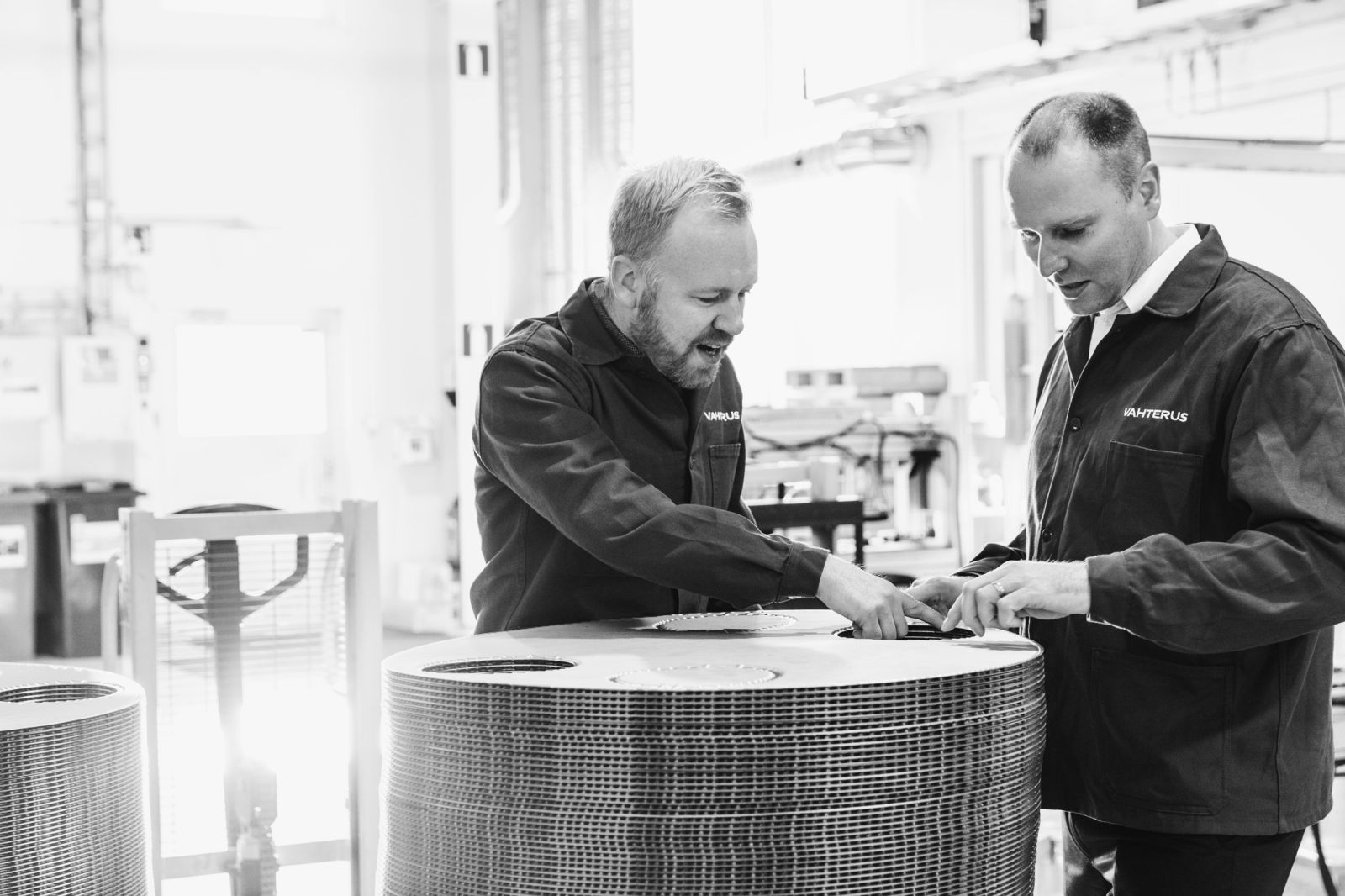
Transform your project with Vahterus Expertise
Interested in working with us? Our team of experts are ready to collaborate with you. Contact us today to embark on a journey towards cost-effective, sustainable and energy-efficient heating solutions.
Discover more of our Customer Stories
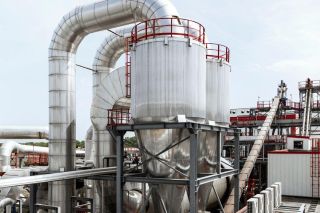
Global Challenges Drive Innovation at Pannonia Bio’s Ethanol Plant
Pannonia Bio's ethanol plant not only leads in green innovation but exemplifies collaborative success. Since 2012, the company has grown into Europe's...

40 MW Ammonia Heat Pumps are Revolutionising District Heating in Sweden
E.ON, one of the world’s largest investor-owned electric utility service providers, installed four GEA heat pumps, each with a heating capacity of...
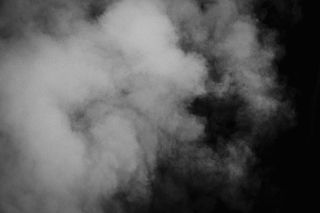
Cryostar’s Saturation System Transforms Truck-Fuelling Stations
Founded in 1972, Cryostar specialises in designing and manufacturing cryogenic equipment. The company offers turbomachines, gas heaters and vaporisers, pumps, turbines as...