The Path to Becoming LNG Experts
Vahterus’ LNG journey began in 2005. Through extensive R&D work and with over 300 heat exchangers delivered to cryogenic LNG applications, we’re now leaders in the field.
Lauri Bastman, Key Account Manager at Vahterus
Every expert was at one time a beginner; everyone starts the journey from the same position of inexperience. This is particularly true of those who are the forerunners of industry. There are no ready-made answers, there are no well-established procedures, and there are no decades of practical experience letting you know what works and what doesn’t. That is, in the beginning.
For us at Vahterus, our journey with LNG properly began in 2005 with Boil-Off Gas heaters. Before that, we had of course worked with Natural Gas in various applications and temperatures, but now we were working close to the liquid tanks and at cryogenic temperatures. The second milestone came a few years later, when for the first time ever, we started working with Liquefied Natural Gas. The heat exchanger in question is still operating well to this day, using cold methane liquid to condense LNG back into a storage tank. The heat exchanger was not a very large one, as they are these days, with only 60 kW of duty, or about 450 kg/h of condensing LNG. But as a brave man once said, sometimes small steps can be giant leaps.
It was certainly that way for us at Vahterus. We proved in practice what we had known for a while: that the original Vahterus Plate & Shell can be adapted and made ideal for LNG applications. This was further proven just a short while later, when we took another step and entered the machinery spaces of LNG-powered vessels by supplying LNG fuel vaporisers under strict Marine Classification Society guidelines.
With our willingness to collaborate on developing tailored solutions, and the several benefits of our technology compared to the more traditional solutions, we were the obvious choice of manufacturer. There are numerous inherent benefits to our basic design, when compared with competing technologies such as Shell & Tube. One of the greatest of these is the small size. This minimises the use of materials to bring down costs, and reduces the footprint – anyone who has visited the machine spaces on a vessel will know that space is at a premium. Since the heat exchanger tends to be one of the largest singular components in an LNG skid, the small size of a PSHE allows for massive space savings.
Unlike a Shell &Tube heat exchanger, a Vahterus LNG vaporiser can vaporise and superheat the LNG inside the same unit, in many cases completely removing the need for a separate superheater. This brings further savings on cost and space, and grants far greater flexibility to skidand piping-layout designers.
Doing something new is of course rarely plain sailing. There are challenges when working with cryogenic LNG, and we ourselves have met some of these over the years as we constantly strive to innovate.
While the round plate is highly resistant to thermal cycles, due to its small size a PSHE unit does not have a large charge or reserve of hot media, such as glycolwater, inside it. Consequently, a poorly designed Plate & Shell unit built without taking the system’s special requirements into consideration can lead to freezing issues and non-functionality of the exchanger. With simulations and data from the field, we have identified the causes and mechanisms behind such potential dangers in our exchangers, and our tailor-made LNG heat exchangers implement several solutions to ensure the best possible functionality in all operating conditions. Our development work has constantly broken new ground and we have several patents pending for cryogenic heat exchange.
But the challenges go even deeper – to the very foundations of heat transfer. As the original inventors of the entire Plate & Shell technology, during the foundation of our company 30 years ago there were no ready-made methods of directly calculating heat-transfer coefficients or other necessary information for even the simplest applications. We adapted the well-established principles of general heat transfer and equations made for other technologies to our own needs based on testing and exchangers, with a dedicated customised testing rig for even more extreme conditions and greater capacities, using cryogenic liquid nitrogen to provide us with more data to supplement our small-scale liquefied nitrogen tests. This data will be further refined and combined with the use of computer simulations to ensure our know-how remains the best in the world, and we are always on the lookout for new possibilities to apply this knowledge in environmentally conscious ways.

Our custom-built LNG heat exchangers implement several solutions to ensure the best possible functionality in all operating conditions. Our development work has constantly broken new ground and we have several patents pending for cryogenic heat transfer.
An exciting new trend in LNG-related applications is the growing number of Cold Recovery systems. The idea behind Cold Recovery is simple: energy has already been applied to liquefy the LNG and store it in cryogenic conditions. This LNG has then been transported elsewhere. If the LNG is simply vaporised and heated for use, its local cooling capacity is wasted. So instead, why not hook up HVAC or refrigerator systems to the LNG vaporisation process? This way, there is no need to expend further energy on creating artificial cold. With our 30 years of experience in the refrigeration industry and natural refrigerants real-world experience. When we introduced LNG applications as possibilities for Plate & Shell, we had to adapt those equations again based on new data. Thanks to the efforts of our extensive R&D programme and years of data from operational heat exchangers, we have now developed our very own fine-tuned custom-built thermal design programme for LNG applications, allowing us to model their thermal behaviour, freezing potential and much more.
Yet work remains to be done. We fully intend to remain at the tip of the spear, leading the technology and market in onshore and marine LNG heat exchangers. This requires further development of brand-new ideas, refining, testing and improving technology, in order to provide the best possible solution to our customers. Our ongoing R&D programme plays a critical role in this, and we continue to invest heavily in it. This spring, we are launching large-scale active testing in our own laboratory for LNG like ammonia and CO2, we have a good understanding of both sides of the Cold Recovery process. This enables us to pool our assets and knowledge on related application development.
The road we have travelled has brought us to the point where we can truly call ourselves experts. We have done countless simulations and tests, have close to 20 years of continuous experience in the field, have delivered over 300 heat exchangers to cryogenic LNG applications, and have been involved in more than half of the current LNG-powered marine vessels on the planet. With this list of merits, we can proudly say we are the industry leaders. Our Plate & Shell technology is not some exotic newcomer on the market, but a well-proven industry standard solution on land and on sea.
This path has only been possible with dedication, hard work and collaboration with our partners and customers, and we look forward to continuing on that road by developing tailor-made solutions for our customers and meeting future challenges.
Read more LNG related content
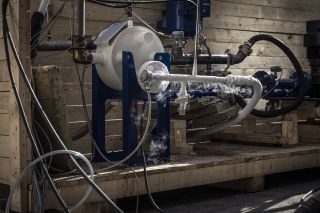
Vahterus solutions for alternative fuels
In a world grappling with rising greenhouse gas emissions, Vahterus emerges as a crucial ally for the maritime industry. As global shipping...
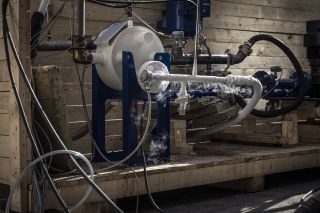
LNG Special Issue
Vahterus’ LNG journey began in 2005. Through extensive R&D work and with over 300 heat exchangers delivered to cryogenic LNG applications, we’re...
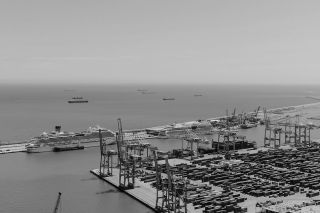
LNGenius: Clever Cold Energy Recovery in Spain’s Ports
Enagas is a company with 50 years’ experience of working with the gas supply, both in Spain and globally. It owns and...